TECHNOLOGY
European Technology covered by more than 30 Patents
EEMCO‘s vertical integration ensures superior SiC crystal quality, starting with high-grade SiC powder sourced and recycled by our subsidiary, SICREATE. Leveraging EBNER‘s 75+ years of furnace expertise, we design and manufacture our proprietary SiC growth furnaces, incorporating advanced technologies like digital twins and Industry 5.0 for real-time process optimization and secure data sharing with customers.
Our SiC manufacturing begins with high-quality powder which is sublimated within EBNER built furnaces, depositing onto a seed crystal to form a boule. The boule is then ground, wafered, and polished, with quality checks at each stage.
This vertical integration, from powder sourcing to wafer production, combined with European supply and R&D partnerships, enables EEMCO to efficiently drive innovation in defect reduction and crystal size expansion beyond 200 mm.
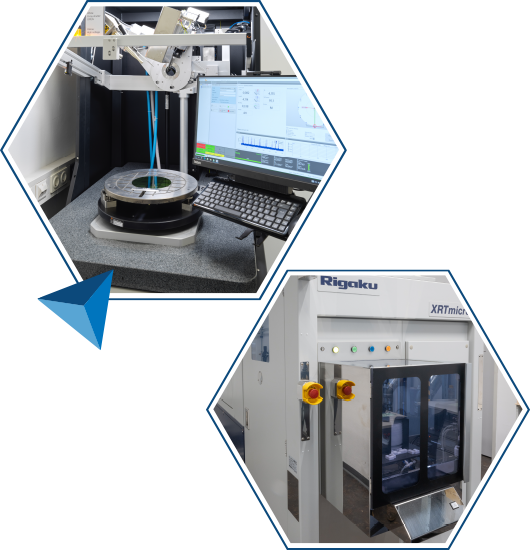
TECHNOLOGY
Our Expertise
We utilize comprehensive defect analysis techniques. This combines, photoluminescence (PL) X-ray tomography (XRT) and KOH etching with assisted AI-powered quantification. This combination allows for a deeper understanding of crystal defects, leading to continuous improvement in crystal quality.
Dislocation Mapping with X-Ray Topography
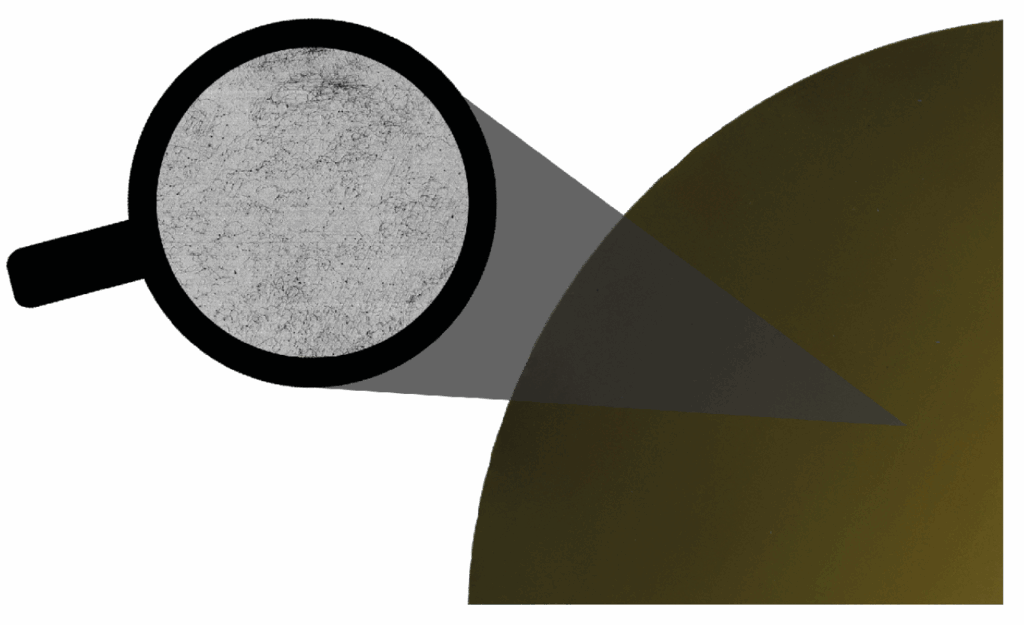
We use a XRTmicron by Rigaku for detailed X-ray topograms, utilizing CuKα- and MoKα-wavelengths and analyzing the (0008) diffraction reflex. This precisely identifies and quantifies Threading Screw Dislocations (TSD) and Basal Plane Dislocations (BPD), ensuring minimal defect density for enhanced device performance.
High-Accuracy Metrology for Surface and Dimensional Control
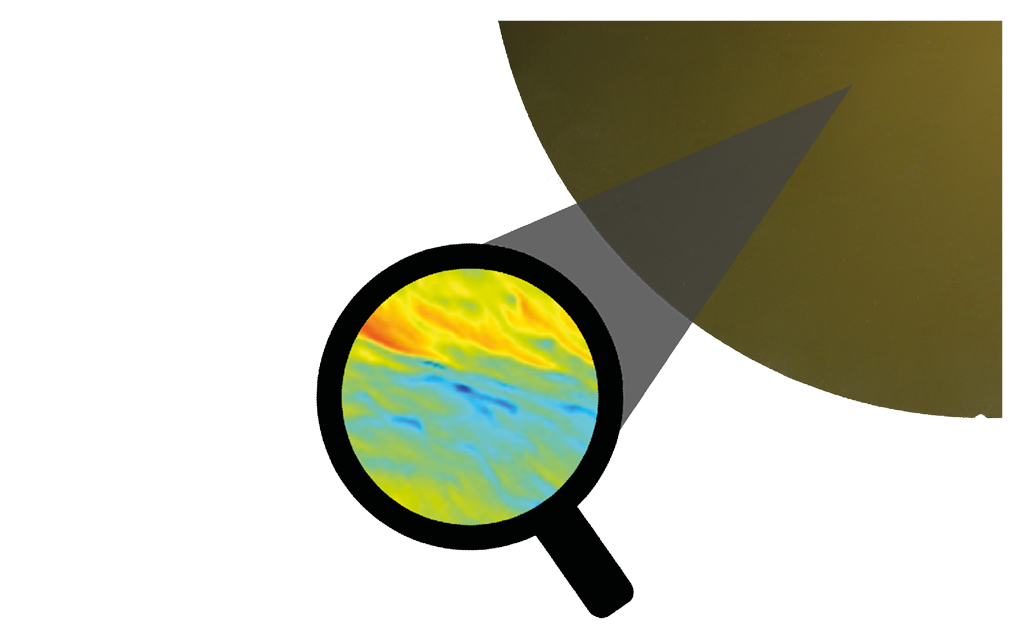
The Sentronics tool enables us to achieve exceptional surface and dimensional precision. White light interferometry measures surface roughness down to Angstroms, critical for optimal epitaxial growth. Spectral coherence detection ensures precise bow, warp, and thickness control.
Automated Defect Counting with KOH Etching and AI
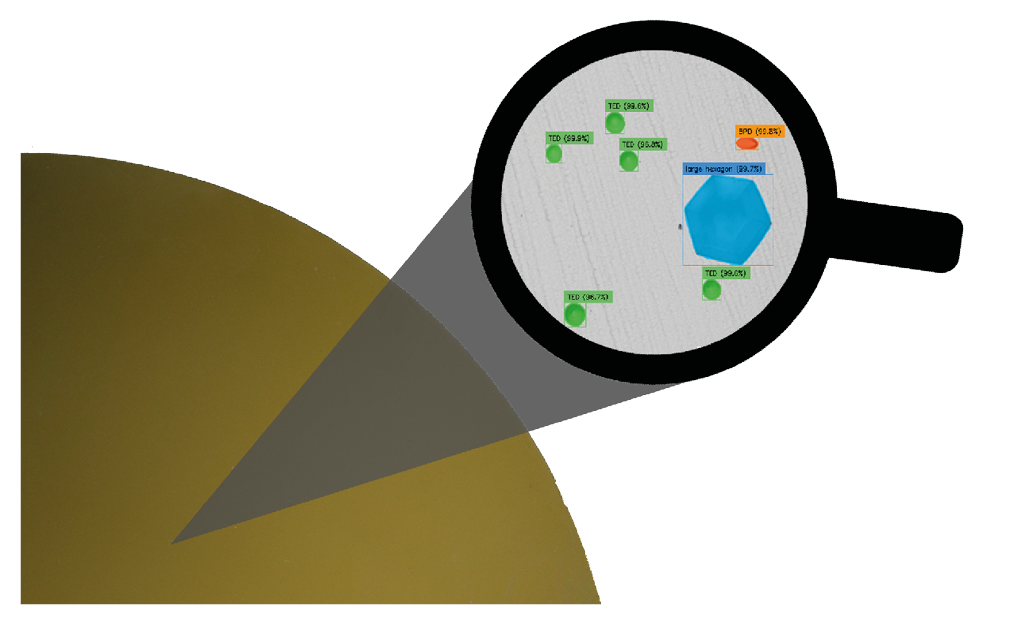
Our process includes KOH etching followed by automated analysis using an Olympus light microscope and our proprietary Artificial Neural Network (ANN) algorithm. This accurately counts and classifies Threading Dislocations (TDs) and BPDs, providing consistent and reliable quality assurance for every SiC ingot and wafer.
Simulation-Enhanced Crystal Growth for Superior Material
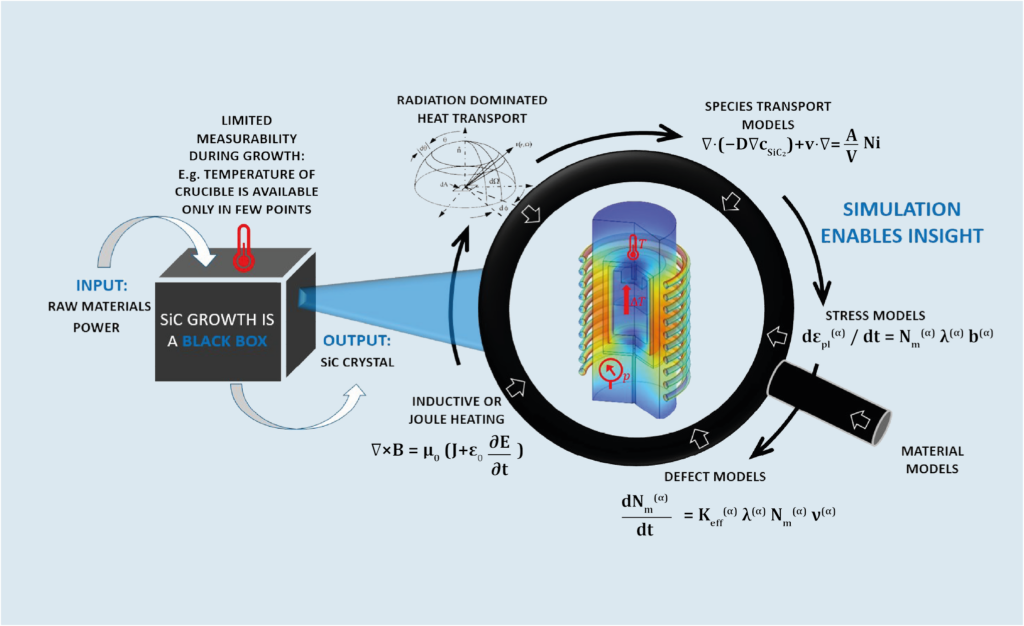
EEMCO utilizes advanced data-driven and physics-based simulation, including COMSOL and custom machine learning models, to optimize our SiC crystal growth. This enables us to fine-tune growth recipes and hot zone geometry, leading to reduced stress and fewer defects for consistently superior material quality.
Our Commitment
Our vision is to produce with 100 % green energy at EEMCO, offering higher quality and competitive pricing. We commit to emphasize renewable energy use and raw material recycling.
MANUFACTURING PROCESS
From Raw Material to Ingot
The SiC manufacturing process begins with high-quality SiC powder, sourced and recycled by EEMCO’s subsidiary, SiCreate. This powder is placed within a crucible inside a specialized furnace, developed and provided by EBNER.
Within the furnace, a seed crystal is introduced, and the SiC powder undergoes a process called Physical Vapor Transport (PVT). Under high temperatures, the SiC powder sublimates into a gas and redeposits onto the seed crystal, gradually forming a larger SiC crystal known as a boule.
Once the boule is grown, it is removed from the furnace. Its outer diameter is then ground and polished, and a „witness wafer“ is extracted for quality analysis. The boule is then sliced into thin discs called ingots using a multi-wire saw. These ingots are further processed and polished into SiC wafers, ready for use in manufacturing power electronics.
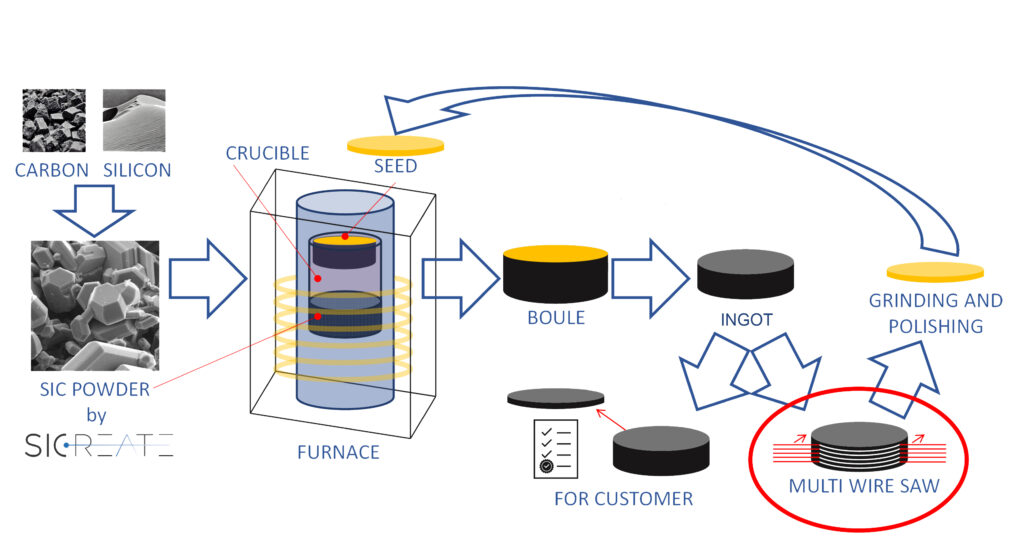
WHY EEMCO?
We are the independent, green and
ISO certified SiC producer in Europe
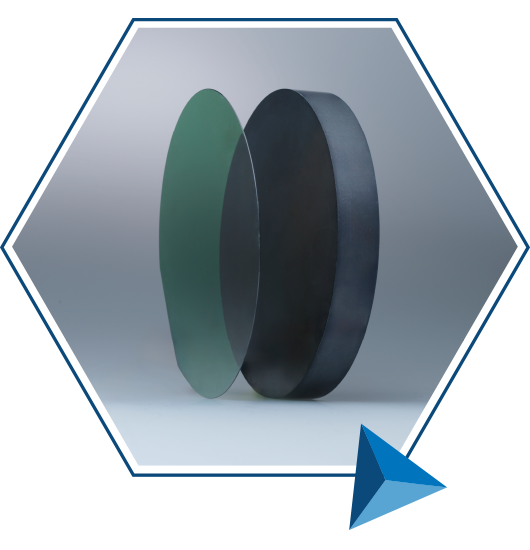
- R&D and pilot line in Austria, zero-emmission volume ramp-up planned in Norway
- Own dedicated process development for high-quality 200 mm seeds
- Comprehensive defect analysis using photoluminescence (PL), XRT, KOH, and AI-powered quantification
- Advanced and automated furnace digitalization
- Close cooperation with different research partners in both academia and industry
- Leveraging 75+ years of EBNER expertise in furnace manufacturing and shared services
- Enhanced furnace technology and component reusability for a greener process